Pengecoran adalah teknik manufaktur dimana bahan (biasanya logam) dilebur dan dituangkan ke dalam cetakan untuk membentuk bagian atau produk tertentu. Proses ini banyak digunakan karena secara efisien dapat menghasilkan geometri kompleks baik dalam skala kecil maupun besar.
Seperti metode produksi lainnya, pengecoran memiliki risiko kegagalan jika tidak dilakukan dengan benar. Kegagalan dalam proses pengecoran dapat terjadi karena kesalahan teknis, material, atau parameter proses yang ditetapkan. Di bawah ini adalah rincian penyebab kegagalan proses pengecoran yang dipecah menjadi beberapa kategori besar.
1. Kesalahan dalam Desain Cetakan
Desain cetakan adalah salah satu faktor terpenting untuk keberhasilan proses pengecoran. Desain cetakan yang tidak tepat meningkatkan kemungkinan terjadinya cacat pada hasil pengecoran.
Misalnya, cetakan dengan saluran penuangan (gate) yang salah dapat mengganggu aliran logam cair. Aliran yang terputus-putus atau turbulen dapat menyebabkan cacat seperti segel dingin dimana lapisan logam tidak terikat dengan baik karena pemadatan dini.
Selain itu, cetakan tanpa ventilasi yang baik dapat memerangkap gas di dalamnya, sehingga menciptakan pori-pori dan gelembung gas pada produk akhir.
2. Material Cair yang Tidak Bersih
Dalam proses pengecoran, kebersihan bahan cair sangatlah penting. Bahan cair yang mengandung kotoran, benda asing, dan oksida dapat menyebabkan inklusi non-logam.
Inklusi ini sering kali tampak sebagai bintik keras atau rapuh yang dapat melemahkan struktur produk. Untuk mengatasi masalah tersebut harus dilakukan proses pemurnian terhadap bahan cair, seperti menggunakan filter khusus sebelum pengecoran.
3. Pengaturan Suhu yang Tidak Tepat
Suhu logam cair memegang peranan penting terhadap kualitas hasil pengecoran. Jika suhu logam cair terlalu rendah, logam akan mulai mengeras sebelum memenuhi cetakan sepenuhnya, sehingga berpotensi mengakibatkan cacat seperti pengisian tidak lengkap dan pengecatan tidak lengkap.
Sebaliknya jika suhu terlalu tinggi, logam cair dapat merusak cetakan, apalagi jika cetakan terbuat dari bahan yang peka terhadap panas seperti pasir. Temperatur yang tinggi dapat meningkatkan oksidasi bahan cair dan membentuk lapisan teroksidasi yang membahayakan integritas coran.
4. Pendinginan yang Tidak Merata
Setelah logam cair dituangkan ke dalam cetakan, pendinginan yang seragam sangat penting untuk menghindari cacat termal. Area yang mendingin lebih cepat dibandingkan area lain dapat mengalami tekanan termal, yang dapat menyebabkan keretakan dan deformasi.
Dalam beberapa kasus, pendinginan yang tidak merata juga dapat menyebabkan cacat berupa penyusutan porositas atau rongga. Kekosongan di dalam produk yang disebabkan oleh kontraksi material selama pendinginan. Untuk mengatasi hal ini, cetakan sering kali dilengkapi dengan sistem pendingin yang menjamin distribusi suhu yang seragam.
5. Tekanan Gas Berlebihan
Gas yang terperangkap di dalam cetakan pada saat proses pengecoran merupakan salah satu penyebab umum terjadinya cacat pada hasil pengecoran. Gas ini dapat dihasilkan oleh udara yang masuk ke dalam cetakan atau melalui reaksi kimia antara logam cair dan bahan cetakan.
Gelembung udara yang terperangkap dapat menyebabkan cacat seperti porositas dan rongga sehingga melemahkan struktur produk. Untuk mencegah hal tersebut maka perlu dirancang cetakan dengan ventilasi yang baik dan menggunakan bahan cetakan dengan permeabilitas gas yang baik.
6. Kualitas Cetakan yang Buruk
Cetakan yang rusak atau tidak dipasang dengan benar dapat mengakibatkan berbagai cacat pada hasil pengecoran. Cacat yang umum terjadi adalah flash, dimana logam cair bocor melalui celah pada cetakan dan membentuk lapisan film yang tidak diinginkan pada permukaan produk. Selain itu, cetakan yang terlalu rapuh dapat retak selama proses pengecoran atau pendinginan, sehingga dapat menyebabkan deformasi pada produk akhir.
7. Kurangnya Kontrol Proses
Kontrol kualitas yang buruk selama proses pengecoran dapat mengakibatkan cacat yang tidak terdeteksi sebelum produk digunakan. Parameter seperti temperatur, tekanan, waktu pengecoran, dan laju pendinginan harus dipantau secara cermat untuk mendapatkan hasil pengecoran yang optimal. Misalnya, waktu injeksi yang terlalu cepat dapat menyebabkan turbulensi pada aliran logam cair, dan waktu injeksi yang terlalu lambat dapat menyebabkan pemadatan dini.
8. Pemilihan Material yang Tidak Sesuai
Jika Anda memilih bahan yang tidak sesuai dengan jenis cetakan atau lingkungan penggunaan, cacat pengecoran dapat terjadi. Misalnya, logam dengan suhu leleh tinggi mungkin tidak cocok untuk cetakan pasir karena dapat melemah atau meleleh pada suhu tinggi. Oleh karena itu, penting untuk memastikan bahwa bahan yang digunakan memenuhi persyaratan proses pengecoran.
9. Faktor Lingkungan
Lingkungan juga dapat mempengaruhi keberhasilan proses pengecoran. Suhu ruangan yang terlalu rendah dapat mendorong pemadatan logam cair, sedangkan kelembapan yang tinggi dapat menyebabkan air dan logam cair bereaksi dan menghasilkan gas, yang dapat mempengaruhi kualitas coran.
10. Ketidaksesuaian Spesifikasi Produk
Kesalahan sering terjadi apabila hasil pengecoran tidak sesuai dengan spesifikasi produk yang diinginkan. Hal ini dapat disebabkan oleh berbagai faktor, termasuk kesalahan dalam desain cetakan, pengaturan parameter proses yang salah, dan cacat yang tidak terdeteksi selama pemeriksaan.
0 Komentar
Artikel Terkait
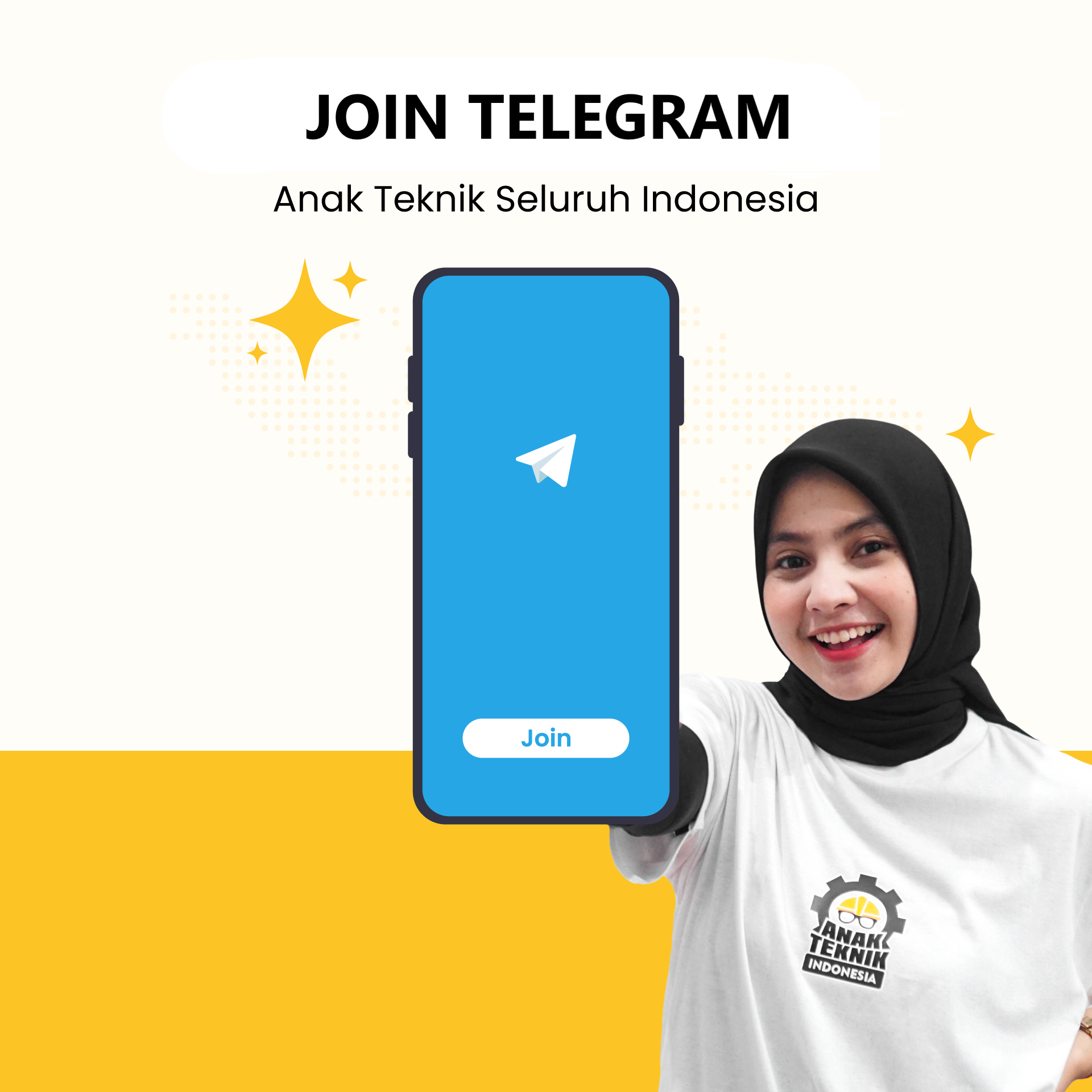