Penggunaan Teknologi PLC (Programmable Logic Controller) dalam kontrol listrik industri memiliki banyak manfaat dan aplikasi yang luas. Berikut adalah beberapa aspek penting dari penggunaan PLC dalam industri:
1. Automatisasi Proses Manufaktur
Penggunaan PLC dalam otomatisasi proses manufaktur memberikan berbagai keuntungan. Dalam proses perakitan produk, PLC berperan dalam mengendalikan robotik dan peralatan otomatis, termasuk pengawasan pergerakan robot, proses pengelasan, pemasangan komponen, dan pengujian produk secara otomatis. Sistem conveyor banyak digunakan dalam industri manufaktur. Untuk mengendalikannya dibutuhkan PLC karena memiliki akurasi terhadap kecepatan, arah, dan penghentian conveyor. Dalam tahap pemrosesan , PLC digunakan untuk mengontrol mesin pemotong dan penggiling.
Kelebihan lain PLC untuk mengatur parameter-proses, seperti suhu, tekanan, dan kelembaban, dengan tingkat akurasi yang tinggi, memastikan konsistensi dan keamanan produk. PLC juga memfasilitasi penjadwalan produksi, waktu siklus, dan alokasi sumber daya sesuai kebutuhan. Selanjutnya, integrasi PLC dengan sensor memungkinkan pengawasan dan tindakan otomatis terhadap ketidaksesuaian. Fleksibilitas dan skalabilitas PLC memungkinkan adaptasi cepat terhadap perubahan kebutuhan produksi, sedangkan integrasi dengan sistem memperkuat kontrol terpusat. Dengan demikian, penggunaan PLC memungkinkan industri merespons perubahan dengan lebih cepat dan efektif.
2. Pemantauan dan Pengendalian Peralatan
Pemantauan dan pengendalian peralatan listrik merupakan aspek krusial dalam lingkungan industri. PLC dapat memantau dan mengendalikan berbagai peralatan listrik. Melalui sistem pemantauan yang terintegrasi, PLC dapat mengumpulkan data secara real-time tentang kinerja peralatan, termasuk suhu, arus listrik, dan status operasional lainnya. Pengendalian otomatis yang disediakan oleh PLC memungkinkan penyesuaian cepat terhadap perubahan kebutuhan operasional. Misalnya, PLC dapat merespons secara otomatis terhadap fluktuasi beban, mengatur kecepatan motor atau pompa, dan menyesuaikan valve untuk menjaga parameter operasional tetap dalam rentang yang diinginkan. Hal ini juga dapat mengurangi konsumsi energi dan memperpanjang umur peralatan.
Selain itu, kemampuan PLC untuk memberikan pengendalian yang presisi membantu menghindari kesalahan manusia. Sistem otomatisasi ini dapat meminimalkan risiko kesalahan, meningkatkan keamanan operasional, dan mengurangi kerugian produksi akibat human error.
3. Pengendalian Sistem Pemanas, Ventilasi dan SC (HVAC)
Penggunaan PLC dalam mengendalikan sistem HVAC di industri memberikan solusi yang efisien dan terukur. PLC dapat diintegrasikan dengan pemanas, pendingin udara, kipas, dan sensor suhu.
Pengendalian suhu merupakan fungsi utama PLC dalam sistem HVAC. PLC dapat diprogram untuk memonitor suhu di berbagai area pabrik atau gedung. Hal ini tidak hanya mendukung kenyamanan pekerja, tetapi juga menjaga suhu optimal yang diperlukan.
Selain itu, PLC dapat digunakan untuk mengontrol kelembaban udara. Pada lingkungan industri yang membutuhkan tingkat kelembaban yang khusus, PLC dapat mengatur operasi perangkat pengontrol kelembaban untuk mencegah kerusakan pada peralatan atau produk. Kontrol sirkulasi udara juga dapat dioptimalkan menggunakan PLC. PLC dapat mengendalikan kipas dan ventilasi untuk memastikan distribusi udara yang merata dan optimal. Sistem ini juga terintegrasi dengan sensor udara untuk memonitor dan menjaga kualitas udara.
4. Pemantauan Kualitas dan Pengendalian Produksi
Penggunaan PLC (Programmable Logic Controller) dalam pemantauan kualitas dan pengendalian produksi menjaga standar kualitas produk dan meningkatkan efisiensi proses produksi. PLC dapat memantau parameter-produksi kualitas secara real-time, termasuk ukuran, berat, keakuratan, dan parameter kritis lainnya.
Melalui sensor dan perangkat pengukuran, data produksi dapat dikumpulkan dan dianalisis secara otomatis. Apabila terdapat penyimpangan dari standar yang ditetapkan, PLC dapat segera merespons dengan mengambil tindakan korektif. Misalnya, jika produk tidak memenuhi ukuran atau berat yang diinginkan, PLC dapat menghentikan atau mengubah proses produksi secara otomatis untuk menghindari produksi barang cacat.
Kecepatan respons ini sangat penting untuk meminimalkan jumlah produk cacat dan mengurangi pemborosan bahan baku. Selain itu, dengan penggunaan PLC, proses produksi dapat dijalankan dengan tingkat konsistensi yang tinggi, menghasilkan produk yang memiliki kualitas seragam.
Pengendalian produksi yang terintegrasi dengan PLC juga memungkinkan pemrograman ulang yang fleksibel jika ada perubahan dalam spesifikasi produk atau peralatan produksi.
5. Pemeliharaan dan Diagnostik
Penggunaan PLC (Programmable Logic Controller) dalam pemeliharaan dan diagnostik bermanfaat dalam memantau kondisi perangkat dan sistem di lingkungan industri. Dilengkapi dengan kemampuan pemantauan dan deteksi kesalahan, PLC memfasilitasi kegiatan pemeliharaan dan diagnosis masalah dengan efisien. Salah satu keunggulan utamanya adalah kemampuan pemantauan kondisi perangkat secara terus-menerus. Data real-time yang terkumpul memberi informasi tentang suhu, tegangan, arus, dan parameter kritis lainnya.
PLC juga dapat diprogram untuk melakukan deteksi kesalahan secara otomatis. Jika terjadi peningkatan suhu pada sebuah motor, PLC dapat mengambil tindakan otomatis, seperti menghentikan operasi. Selain itu, kemampuan PLC untuk memantau kesehatan sistem secara keseluruhan memastikan bahwa seluruh sistem berfungsi sesuai spesifikasi tanpa adanya tanda-tanda kegagalan.
PLC juga mendukung pemeliharaan terjadwal dengan memanfaatkan pemantauan kondisi perangkat dan sistem. Ini memungkinkan penjadwalan pemeliharaan preventif pada waktu yang paling tepat, menghindari kegagalan yang tak terduga dan mengurangi downtime produksi. Ketika terjadi masalah atau gangguan, PLC menyediakan informasi untuk identifikasi sumber masalah dengan lebih efisien, mempercepat proses pemulihan.
Penggunaan PLC juga membantu mengurangi downtime produksi karena kegagalan perangkat atau sistem. Tindakan cepat yang diambil setelah deteksi masalah dapat mempercepat proses pemulihan. Selain itu, PLC dapat menyimpan data historis untuk analisis jangka panjang kinerja perangkat dan sistem.
0 Komentar
Artikel Terkait
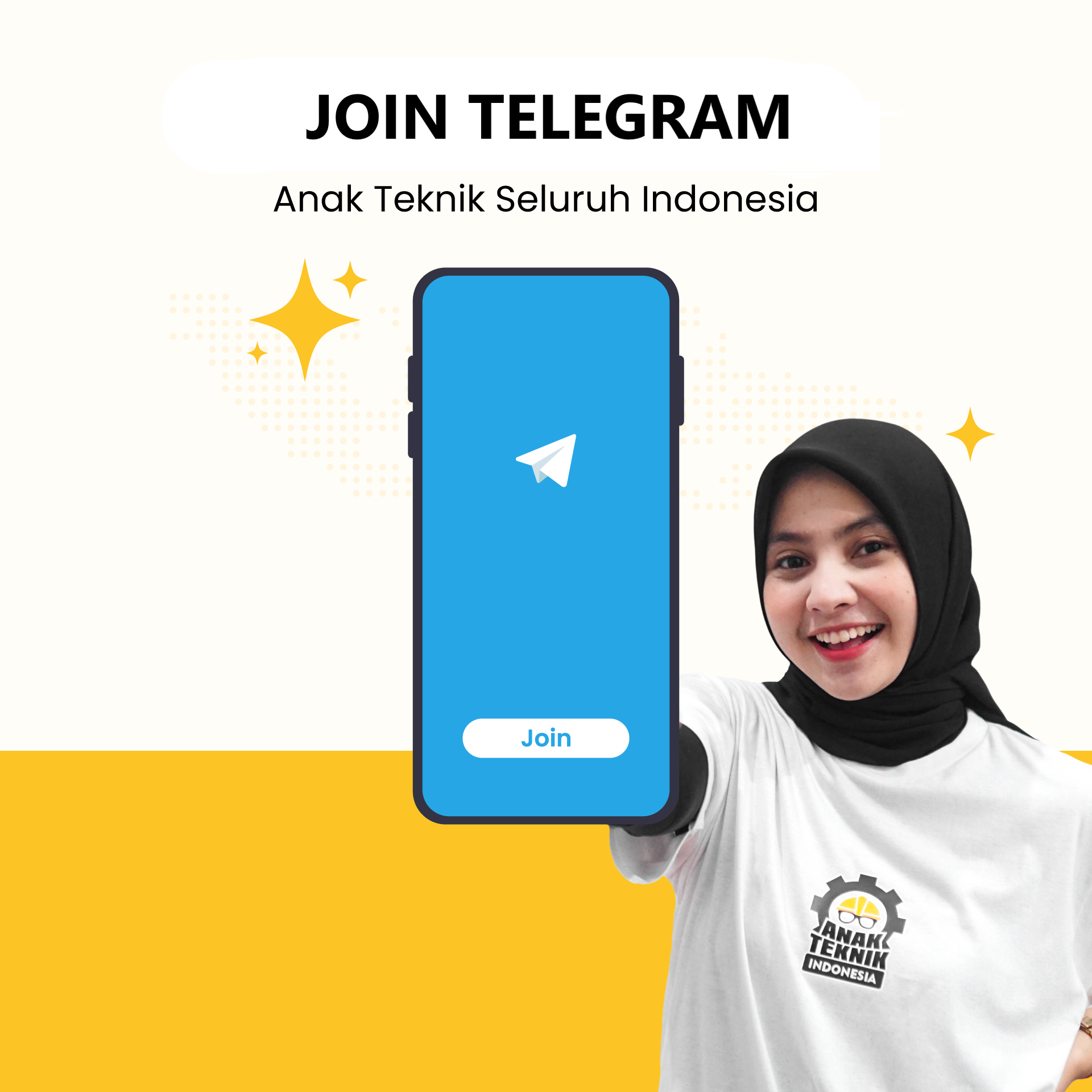